Table of content
1. What is Equipment Hoarding?
2. Why Equipment Hoarding Happens?
3. How Equipment GPS Trackers Help
Key Takeaways
Keeping equipment within specific job sites and not sharing across projects happens often and can be a costly problem for businesses. In fact, hoarding equipment on site can be an unexpected expense that slowly eats away at profit margins. Not only does it reduce ROI on expensive equipment but can also mean loss of revenue from jobs that are cancelled or delayed due to resourcing issues. GPS equipment trackers are key to understanding why equipment hoarding happens and how to solve for it.
What is Equipment Hoarding?
An expensive concern for those managing construction and infrastructure projects, equipment hoarding involves trucks, bulldozers, and other pieces of machinery going unused at a specific location. This can happen for multiple reasons, including:
- The requirement for the asset to be used later in the project
- Avoiding the expense of renting an asset if it's not available when it's needed on site
- Fleet managers are not properly monitoring equipment use and maintenance
- Equipment unexpectedly breaks down and has not been repaired
Or maybe equipment hoarding is more intentional. Perhaps a site foreman is storing up equipment not currently in use knowing there’ll be a need later. Or maybe a piece of equipment was unintentionally left at a job site where the work has been paused, leaving it unused and susceptible to theft. Without the eye of telematics and GPS equipment and asset tracking, a business may not have a realistic picture of their sites.
Whatever the reason, equipment hoarding can cause significant delays to projects and increase operating costs.
Why Equipment Hoarding Happens
Equipment hoarding can happen for multiple reasons. Here are three of the primary examples:
Scenario 1: A site manager, who has been incentivised to complete a job by a certain date, orders more equipment than is necessary. This leaves equipment underutilised and forces other site managers to rent equipment elsewhere, adding additional costs to those projects.
Scenario 2: Your equipment manager prices internal tools and equipment rentals on a lump sum calculation verses a period-of-time charge. While this internal pricing structure is simple to manage, it encourages hoarding by removing the incentive to return the equipment in a timely manner.
Scenario 3: A job hits a critical delay forcing all work to stop for an extended period of time. The fleet or equipment manager isn’t informed of the delay and equipment sits idle on a construction site for days, weeks or even months.
When equipment is hoarded it can impact the bottom line of your business in many ways including:
- Unnecessarily renting equipment that’s currently not in use in your own fleet
- Over bidding jobs by inflating the equipment rental costs for the project
- Job completion delays that increase labor costs and prevent new projects starting
How Equipment GPS Trackers Help
One of the best ways to reduce equipment hoarding is to have equipment GPS trackers installed. This way, you can easily track the equipment location using cloud-based software. Foreman and managers have visibility into assignment and available inventory from wherever they are located.
The software is updated in real time with information about equipment location, utilization and maintenance requirements giving teams complete visibility into available inventory and underutilised assets. Equipment trackers are also beneficial in these areas:
Reduce Unplanned Maintenance: One of the biggest expenses with construction equipment is unplanned maintenance and downtime. Understanding where your equipment is located and how it’s being used can help ensure regular inspections are conducted, cutting down on unplanned downtime, which can delay projects and increase costs, especially with emergency maintenance usually coming at a premium. The use of GPS equipment trackers helps workers to maintain equipment by digitising processes and ensures that maintenance records are up to date and schedules followed.
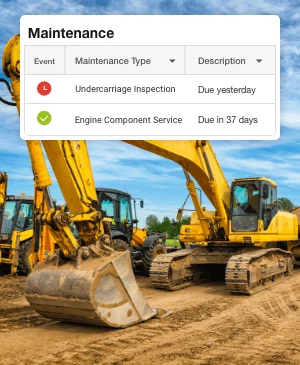
Increase Productivity: When equipment is hoarded, other teams do not have what they need to get the job done, bringing productivity to a stand-still. Technology can help keep your workforce active and engaged by reducing downtime caused by shortages in equipment and tools.
The use of equipment tracking provides teams with visibility across equipment inventory so they can make quick decisions on how to move resources across job sites. Simply looking up the tracking information will show in detail where the nearest available or idle asset is located.
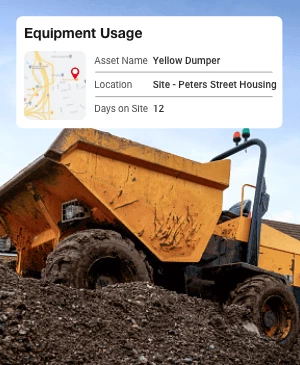
Ensure Compliance: It’s important that your team have access to properly maintained equipment and have the ability to report faults and safety concerns quickly and easily. Digitising this process enables you to easily keep accurate and up-to-date safety records that help you stay compliant with regulations.
In the construction industry and other areas of manual labor, properly maintained equipment and tools can save lives, time, and money for many organisations.
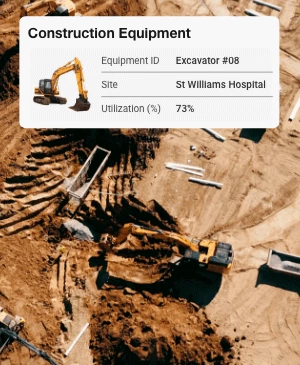